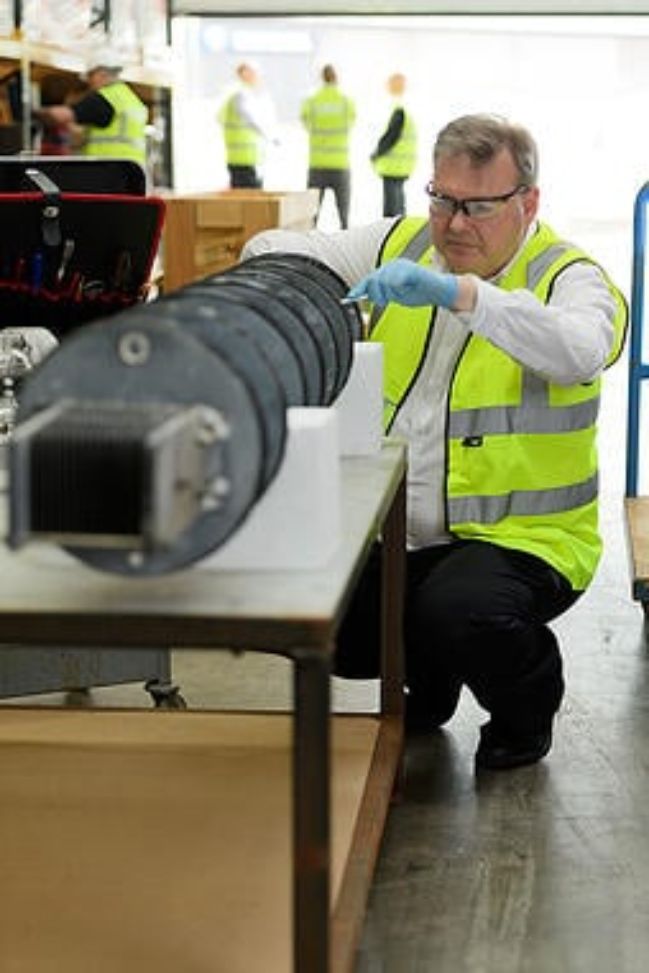
An investment in drinking water and wastewater systems is undertaken to protect public health and the environment. The decision to move ahead on a capital project is one that should not be taken lightly. Whether you are designing a new facility or upgrading an older site, any capital investment, should include the implementation of measures to protect that capital investment. The most effective way to protect an equipment purchase is to follow manufacturer-recommended maintenance and service procedures and schedules. Download our Checklist using the form on this page to keep your equipment in tip top shape.
An equipment purchase is effectively the start of a long relationship between the purchasing company and manufacturer, going well beyond the installation, start-up and commissioning of a system. As a result, it’s important to focus on the service and maintenance a manufacturer offers throughout the life of the equipment. A simple review of the service offerings will help ensure a partnership with a manufacturer that understands what is required to effectively support their system.