Chromium plating, or chrome plating, is a widely utilized process for enhancing the durability, corrosion resistance, and aesthetic appeal of metal and plastic surfaces. The chrome plating process is heavily used in the automotive, aerospace and consumer products industries. For example, the process of plating is used in the surface finishing of automobile parts such as bumpers, wheel rims, and interior trim/surfaces; airplanes parts and components; coated brass parts in the food and beverage sector, and household items such as fixtures, water taps and fittings, appliances and even furniture.
Offering Trivalent Chrome Plating Anodes: A Safer Alternative
The chrome plating process: Hexavalent vs. Trivalent chromium plating
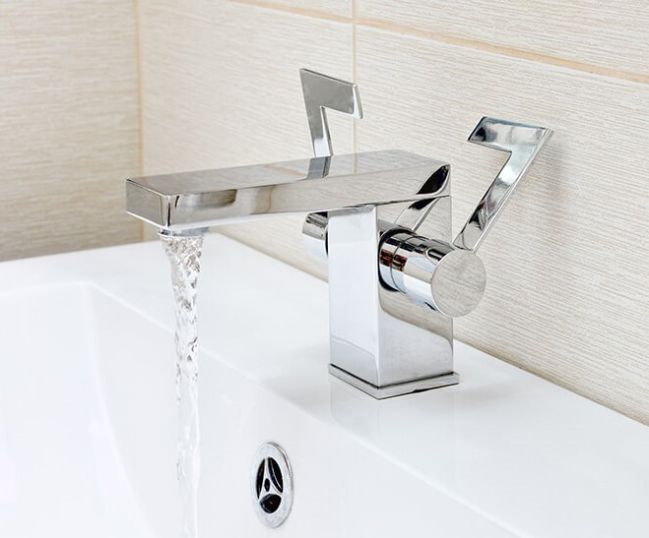
chrome plating of household fixtures
The traditional process of chrome plating relies on hexavalent chromium (VI) derivatives, such as chromium trioxide. Its use poses several environmental and health concerns, as chromium (VI) is carcinogenic and authorized with restrictions. The harmfulness of chrome (VI) has prompted a shift towards safer alternatives to be used globally. Legislative regulations are being implemented in many regions, including Europe and the United States, to replace the use of hexavalent processes in favor of less dangerous ones.
The toxicity of chrome (VI) has prompted a shift towards safer alternatives. For several decades, De Nora GreenChrome™ anodes have been used as a viable solution for trivalent decorative chrome plating, offering many advantages over their hexavalent counterparts. They are safer to use, have high durability, use less energy, and are specifically designed to preserve the integrity of the chromium (III) bath, preventing its oxidation to chromium (VI). Additionally, Greenchrome has been qualified as a top choice for almost all major chemistry suppliers’ trivalent plating baths.
De Nora GreenChrome™ insoluble anodes for trivalent chromium plating baths:
- Are dimensionally stable, highly conductive, and use less energy,
- Provide more throwing power for hard-to-reach areas,
- Have a stable metallic structure provides uniform current distribution and, therefore, more uniform plating over the life of the anode,
- Can replace hazardous lead-based anodes to eliminate an environmental, health and safety hazard,
- Have titanium structure-based anodes which are lighter for ease of installation and removal
- The anode structures can be refurbished (repaired and/or recoated) to reduce costs.
GreenChrome™ anodes are compatible with major chemistries and available in complex solid sheet or mesh structures.
How does the trivalent chromium plating process work?
The process of chrome plating is a galvanic one. Chromium is deposited electrochemically to the surface of an object, previously treated to obtain a Ni undercoat (see equations below),
Cr (III) + 3 e- → Cr (0) (1) cathode
2H2O → O2 + 4e- + 4H+ (2) anode
Specifically, in the electrochemical cell the object that undergoes chrome plating works as a cathode (1). On the other side, an inert material, often activated titanium with a mixed metal oxide coating, is used as an anode (2). The item is then immersed in an electrolyte made of a trivalent chromium (III) plating solution containing dissolved chromium (III) salts for the specific plating bath. During this stage, called electrodeposition or electroplating, the dissolved chromium (III) cations are reduced to chrome (0), which deposits on the surface of the object and builds up the typical metallic coating. At the anode side, water is oxidized to oxygen.
In conclusion, De Nora Greenchrome™ anodes have emerged as a safer and more sustainable alternative to hexavalent chrome plating.